L'extrusion dans tous ses états
Avec l’essor des matériaux polymères, le procédé d’extrusion s’est imposé comme un procédé incontournable pour la mise en œuvre de ces derniers, avec en particulier un développement de la technologie double vis (co-rotatives ou contra-rotatives interpénétrées). Transformer, associer, mélanger, structurer, modifier, recycler, purifier les polymères nourrissent la créativité des chercheurs de l’IMP. La quête permanente de développer des matériaux polymères via des procédés plus verts a permis de s’adapter aux contraintes environnementales et sociétales.
Assimiler l’extrudeuse à un réacteur chimique continu va ainsi permettre de réaliser des réactions en milieu visqueux et en absence de solvant. Contrôler et optimiser le profil des vis, le choix des conditions d’extrusion (température, pression, temps de résidence entre autres), le mode et l’ordre d’introduction/injection des réactifs selon leur nature ouvre la voie à une grande modularité de l’extrusion réactive. Dès lors, polymérisation, copolymérisation, modification chimique, compatibilisation/nanostructuration de mélanges de polymères, élaborations de matériaux hybrides et nanocomposites peuvent être envisagés. Pour illustrer nos travaux les plus récents dans le domaine de l’extrusion réaction, citons la synthèse in situ des polyimides (PI) thermostables dans des matrices thermoplastiques. Grâce à l’association chimie et cisaillement, il est possible d’obtenir une dispersion sub-micronique de la phase polyimide, avec un diamètre moyen des nodules de 200 nm pour toutes les concentrations de PI contrairement à l’obtention de tailles micrométriques quand le même matériau est préparé par simple mélange à l’état fondu (Figure 1).
Figure 1 : Structure du polyimide et morphologies obtenues dans un système PP/PI par simple mélange (MEB central) ou in situ par extrusion réactive (MEB de droite).
Composition PP/PP-g-MA/PI 40/30/30.
En outre, l’IMP a développé une expertise autour de la micro/nano-structuration des polymères par le procédé de coextrusion (classique et/ou par assemblage forcé). Il s’agit d’une technologie innovante et versatile puisqu’elle permet d’obtenir une architecture spécifique en fonction des applications visées pour des domaines aussi variés que stratégiques (l’emballage, l’automobile, l’aéronautique, la domotique, la plastronique, l’optique non linéaire et smart materials avec systèmes de récupération d’énergie, les antennes, les structures pour la protection des cellules photovoltaïques ou capteurs pour le blindage/l’absorption de pollution électromagnétique). Des structures multi-micro/nanocouches (micro/nano-architecturés) sont alors élaborées sans compatibilisant facilitant in-fine leur séparation et recyclabilité post-consommation dans une approche de « Recycling by Eco-design ». Depuis plus de 20 ans, la pierre angulaire de notre recherche a trait à la compréhension et modélisation des phénomènes interfaciaux durant le procédé permettant d’obtenir des multi-micro/nanocouches avec ou sans chimie. L’objectif ultime consiste en la compréhension et la modélisation rhéologique des phénomènes multiphysiques et multi-échelles mis en jeu lors de l’élaboration de ces matériaux. Les phénomènes mis en jeu lors de ce procédé sont particulièrement complexes car ils impliquent de façon couplée des aspects hydrodynamiques avec des cinématiques d’écoulement en cisaillement et en élongation. A ce stade, intervient également le phénomène de compatibilisation physique et/ou chimique aux interfaces/interphases et de cristallisation dans les milieux confinés. Evidemment l’impact des paramètres liés aux interactions matériaux/procédé est un axe majeur de nos travaux.
Figure 2 : Schéma de principe de la coextrusion multinanocouches avec le système développé à l’IMP avec un design home-made d’éléments multiplicateurs et de filières de coextrusion.
D’autre part, l’IMP développe un axe de recherche qui vise à coupler le procédé continu d’extrusion et les fluides supercritiques, plus particulièrement le CO2 pour répondre aux enjeux sociétaux et environnementaux tels que le recyclage ou l’allègement par exemple. Pour cela le laboratoire s’est équipé d’une plateforme expérimentale FluSCritEx (pour Fluide Super Critique et Extrusion) qui propose des équipements adaptés aux conditions opératoires du CO2 supercritique et à celles d’extrusion des polymères. Dans ce cadre, diverses études ont démontré l’efficacité du CO2 pour décontaminer et purifier des matériaux post-consommation, permettant d’obtenir des matières recyclées d’une grande très grande pureté. Le défi actuel consiste à transposer ce procédé discontinu à un procédé continu par extrusion. Les points clés sont bien sûr techniques, nécessitant l’adaptation du matériel aux conditions de pression, et expérimentaux, mais aussi scientifique pour cerner et maitriser les mécanismes physiques et physico-chimiques intervenants dans les phénomènes de diffusion, solubilisation et transport de matière dans le procédé d’extrusion. Le CO2 est également largement utilisé comme agent d’expansion dans les mousses polymères, nécessitant une maîtrise des formulations, des conditions opératoires et des mécanismes de nucléation et d’expansion, ainsi qu’une adaptation des équipements et une étude précise des échanges thermiques pour contrôler la dépressurisation. Enfin le CO2 est également utilisé comme monomère ou agent de fonctionnalisation pour ajouter des fonctions polaires à des polymères apolaires par post-modification en extrudeuse. L’originalité des travaux menés au laboratoire a consisté à transposer cette réaction au procédé continu d’extrusion réactive qui permet de maximiser les échanges entre réactifs dans ces réactions en milieux hétérogènes et donc de s’affranchir de l’utilisation des solvants.
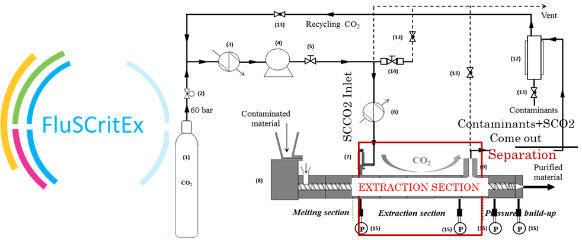
Figure 3 : Schéma de principe de la décontamination par CO2 SC en continue en extrusion